What is Porosity in Welding: Common Resources and Reliable Solutions
The Scientific Research Behind Porosity: A Comprehensive Overview for Welders and Fabricators
Comprehending the complex devices behind porosity in welding is important for welders and producers pursuing impressive workmanship. As metalworkers explore the depths of this sensation, they uncover a globe governed by different aspects that influence the development of these minuscule gaps within welds. From the structure of the base products to the complexities of the welding process itself, a plethora of variables conspire to either intensify or alleviate the existence of porosity. In this thorough overview, we will certainly unravel the science behind porosity, discovering its effects on weld top quality and introduction progressed strategies for its control. Join us on this journey via the microcosm of welding imperfections, where precision meets understanding in the pursuit of flawless welds.
Understanding Porosity in Welding
FIRST SENTENCE:
Evaluation of porosity in welding exposes vital insights right into the stability and quality of the weld joint. Porosity, characterized by the visibility of tooth cavities or spaces within the weld steel, is a common issue in welding processes. These voids, otherwise appropriately addressed, can jeopardize the structural integrity and mechanical residential or commercial properties of the weld, causing possible failings in the completed item.
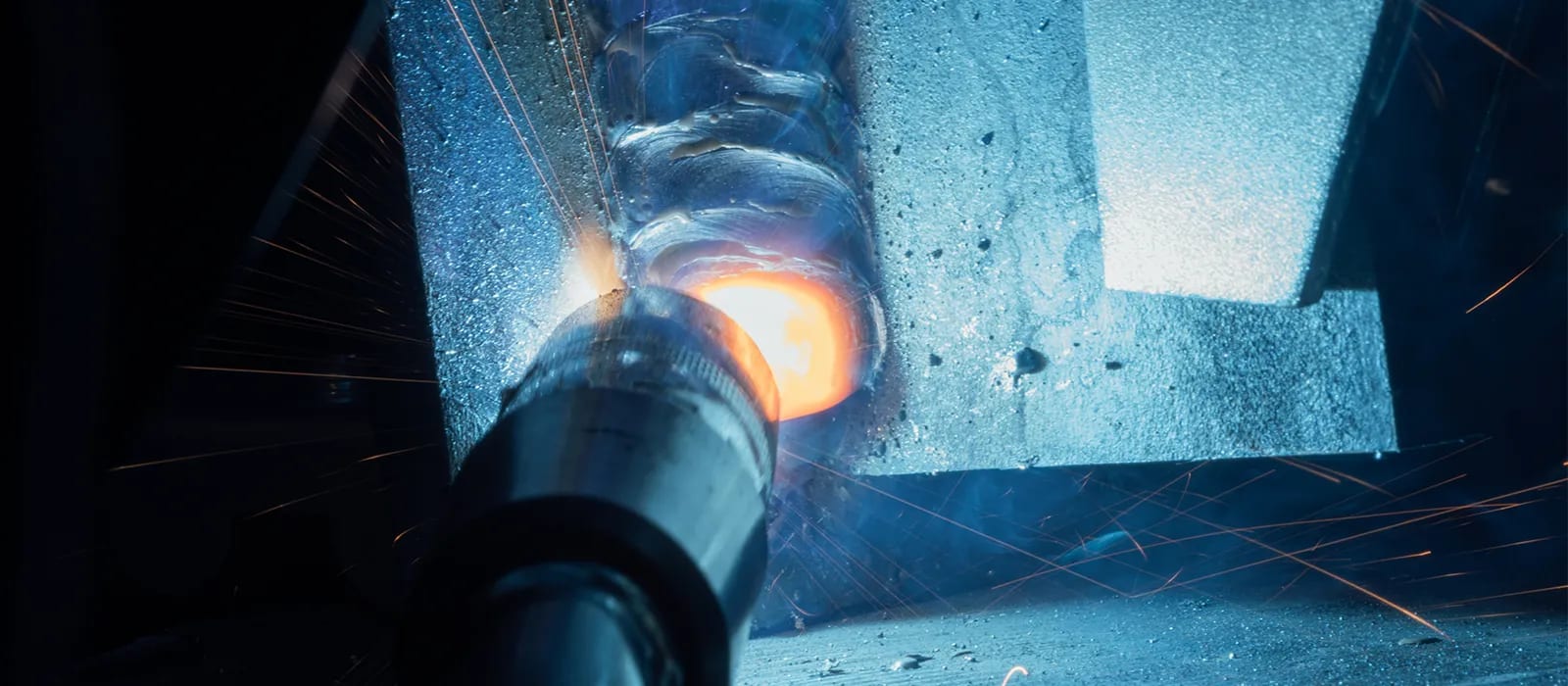
To find and quantify porosity, non-destructive testing approaches such as ultrasonic testing or X-ray examination are frequently used. These strategies allow for the identification of internal flaws without endangering the integrity of the weld. By evaluating the size, form, and distribution of porosity within a weld, welders can make enlightened choices to boost their welding processes and attain sounder weld joints.
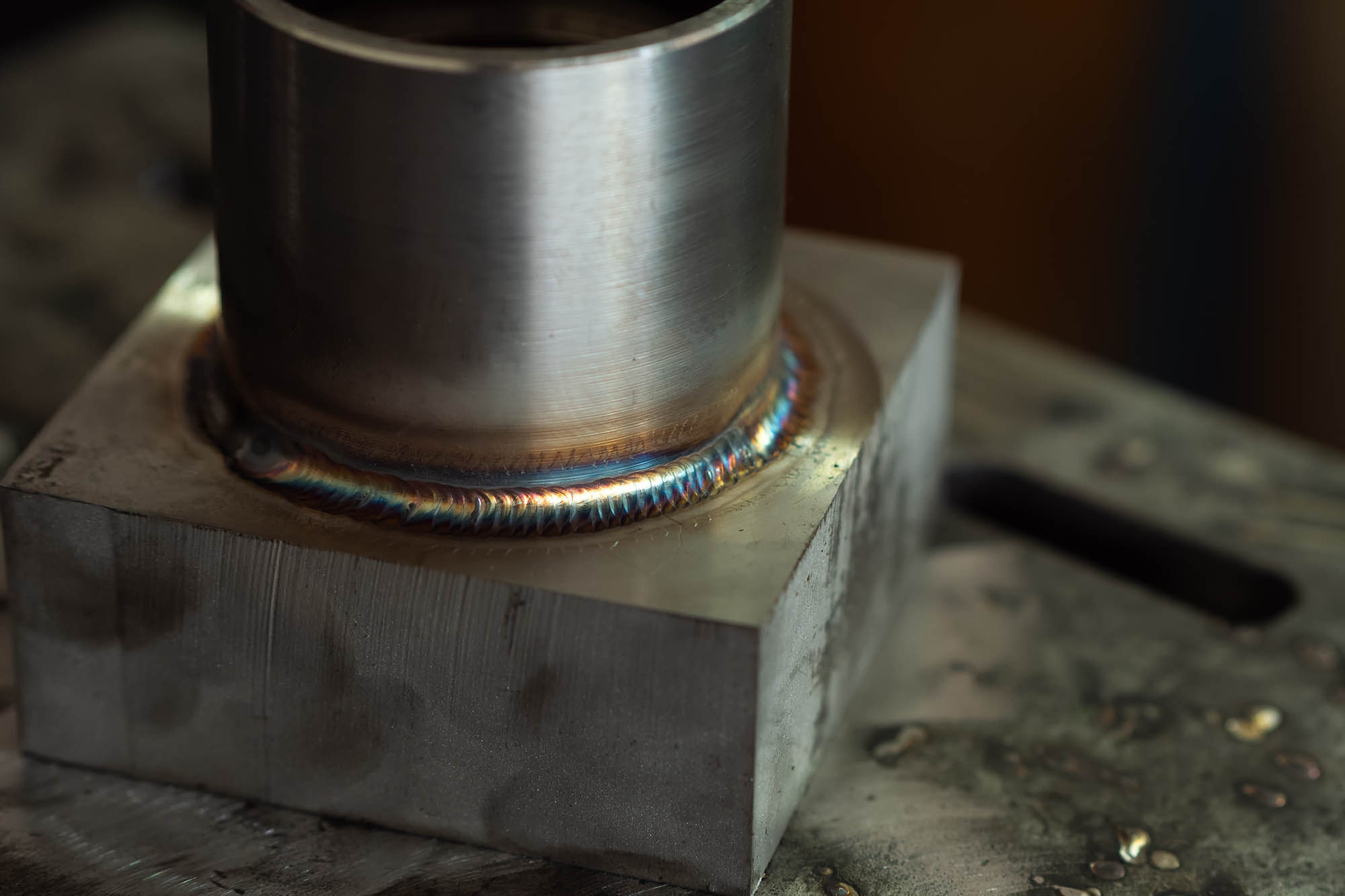
Variables Affecting Porosity Formation
The incident of porosity in welding is affected by a myriad of variables, ranging from gas securing effectiveness to the complexities of welding parameter settings. Welding criteria, including voltage, present, take a trip speed, and electrode type, additionally impact porosity formation. The welding method used, such as gas metal arc welding (GMAW) or shielded steel arc welding (SMAW), can affect porosity development due to variations in warm circulation and gas coverage - What is Porosity.
Effects of Porosity on Weld High Quality
The existence of porosity also weakens the weld's resistance to deterioration, as the caught air or gases within the spaces can react with the surrounding environment, leading to degradation over time. In addition, porosity can impede the weld's ability to withstand stress or influence, additional jeopardizing the total high quality and reliability of the bonded structure. In essential applications such as aerospace, vehicle, or structural building and constructions, where security and toughness are critical, the detrimental results of porosity on weld high quality can have severe effects, highlighting the relevance of lessening porosity through appropriate welding techniques and treatments.
Strategies to Reduce Porosity
In addition, using the suitable welding specifications, such as the right voltage, existing, and take a trip rate, is critical in protecting against porosity. Keeping a regular arc length and angle during welding additionally assists lower the possibility of porosity.

Additionally, choosing the ideal protecting gas and maintaining proper gas flow rates are essential in minimizing porosity. Using the appropriate welding strategy, our website such as back-stepping or using a weaving activity, can likewise assist distribute warm evenly and reduce the opportunities of porosity development. Last but not least, ensuring correct air flow in the welding atmosphere to get rid of any kind of possible resources of contamination is important for achieving porosity-free welds. By executing these techniques, welders can properly lessen porosity and produce high-grade welded joints.
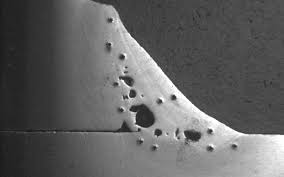
Advanced Solutions for Porosity Control
Implementing innovative technologies and ingenious approaches plays a critical function in achieving exceptional control over porosity in welding procedures. Additionally, utilizing innovative welding techniques such as you could try this out pulsed MIG you can check here welding or customized ambience welding can also aid reduce porosity problems.
One more innovative option entails using advanced welding devices. For instance, using tools with integrated features like waveform control and advanced power sources can improve weld top quality and lower porosity risks. The application of automated welding systems with exact control over criteria can considerably reduce porosity defects.
Furthermore, including advanced monitoring and evaluation innovations such as real-time X-ray imaging or automated ultrasonic testing can aid in finding porosity early in the welding process, enabling immediate restorative actions. Generally, incorporating these advanced options can considerably enhance porosity control and enhance the overall high quality of welded components.
Final Thought
To conclude, understanding the scientific research behind porosity in welding is vital for welders and makers to produce high-quality welds. By identifying the variables affecting porosity formation and implementing techniques to reduce it, welders can improve the total weld quality. Advanced remedies for porosity control can better enhance the welding process and guarantee a solid and trusted weld. It is essential for welders to constantly enlighten themselves on porosity and apply ideal techniques to accomplish ideal outcomes.